Maintenance Made Easy with connectavo
Whether You're Dealing with Fleet Vehicles or a Machine Hall, Efficient Maintenance Preserves the Value of All Types of Machinery System.
This enables running times to be extended, operating costs to be minimized and productivity to be increased. Sustainability is a factor too. With connectavo, mechanical engineering company WAFIOS in Reutlingen is offering a software solution for comprehensive maintenance jobs.
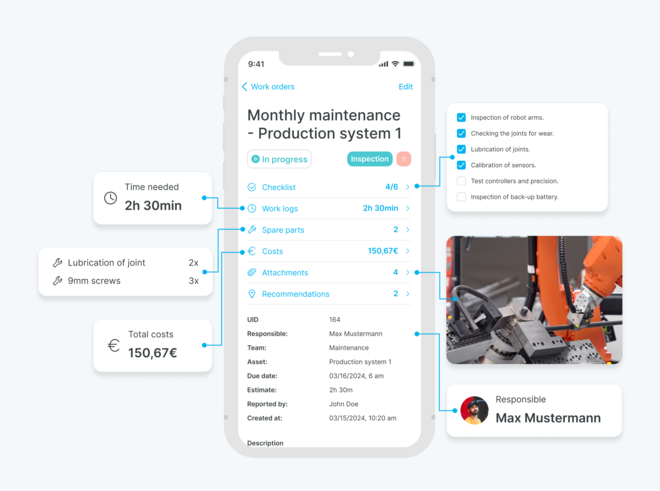
Maintenance has been an important issue in industry for many years now. For some companies, it is absolutely vital that their operating equipment and infrastructure demonstrates a high level of availability. This is why WAFIOS AG from Reutlingen purchased the connectavo maintenance platform in 2019 and set about developing it further.
"Our main focus was on offering our machine customers a flexible solution for their maintenance jobs. Besides, we have the same requirements ourselves when it comes to our own machinery," explains Dennis Griesinger, Head of Digital Services at WAFIOS. "We control over 500 machinery systems in mechanical production facilities for manufacturing components for our machines and tools at several locations within Germany. When we talk about maintenance software, we understand the requirements that have to be met day after day."
Comprehensive maintenance does not stop at the machine
connectavo goes way beyond machine and machinery system maintenance. The software also covers building, asset and fleet vehicle management. Machine and machinery system maintenance includes, for example, the planning, coordination and analysis of routine actions such as machine lubrication, wear inspections and the like. All actions can be documented. It is also possible to record fault messages automatically with push notifications.
Building and asset management relates to the entire infrastructure including, e.g., heaters, crane systems, compressed air systems or elevators. Functions are also available for assets relating to safety such as fire extinguishers, fire doors or extinguishing systems. Maintenance work can also be coordinated across multiple sites. Fleet vehicle management can be used to plan service work and repairs for all vehicles. This includes, for example, reminders about legally prescribed main inspections. Corresponding documentation can be created here too.
Griesinger: "connectavo is a holistic solution for industrial companies for both scheduled and unscheduled events. No area is left out because the software can be populated with such a wide variety of assets."

Independent thanks to the app
The software shows the company's infrastructure as a tree structure. Documents, maintenance plans, images, etc., can be saved for every item. Users can individualize assets and assign them to specific responsible employees. There is also an option to conduct various analyses, e.g., to compare individual assets in terms of their downtimes and costs. Users can save all the actions that have been taken in histories.
Another innovative feature is a self-learning knowledge database with automatic recommendations.
connectavo is a cloud-based solution. The servers are located in a dedicated data center inside Germany and meet the highest standards of security. Users log in to the system via a browser or a smartphone app (Android, iOS). With the latter, users can log in from wherever they happen to be. The system sends individual reports as required so the responsible people are always kept up to date. Conversely, reports can be sent to the system or processes can be initiated from outside too, such as damage reports or requests to purchase consumables.
Individual adaptations
The user simply has to add their data to the prepared file. A CSV file is used for larger data packets. "If large volumes of data are involved, we support customers during the onboarding process," adds Griesinger. "But the software has been structured in such a way that users can basically maintain their own data. They can grant permissions and rename categories, for example – in short, they can customize the system to meet their needs." Documents can also be saved as "requiring approval", which means they will always be available.
Since the platform was acquired, the development team has been housed at WAFIOS head office in Reutlingen. At present, a 14-strong team is responsible for further developing the software and providing support. "New customers will be investing in a futureproof solution for their work of today and of tomorrow," says Dennis Griesinger. "We would be happy to present the system online to anyone who is interested. We can also introduce people to the software in person in one of our plants or give them access on a trial basis."
You can also read our article in ReThink Industry.
Increase your productivity through efficient methods.
Try connectavo out free of charge!